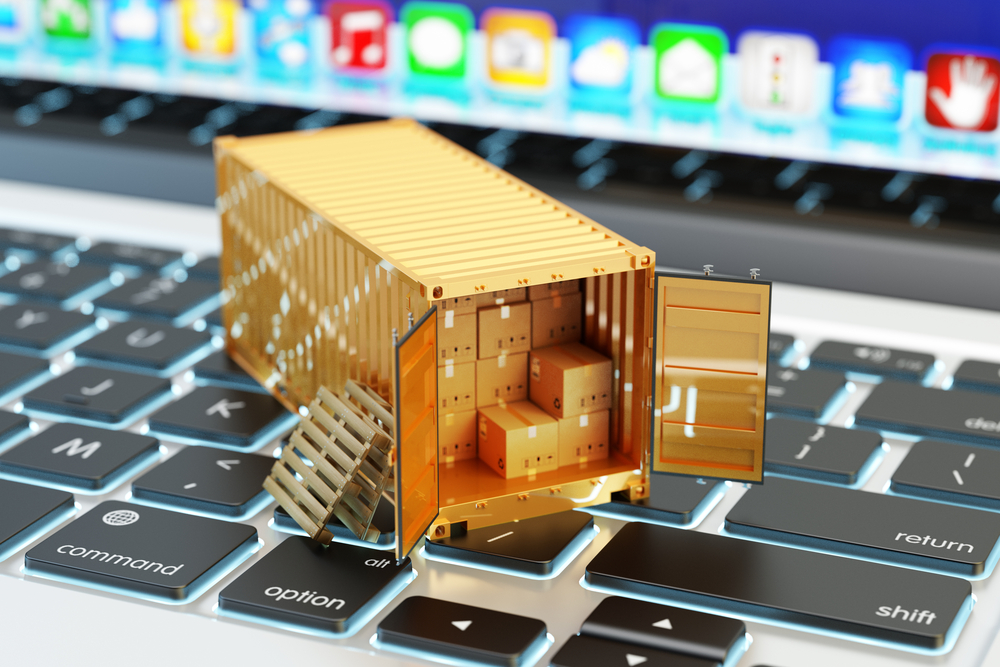
Manufacturing a brand new product can be exciting but there are also many things you need to watch out for to produce a high quality product.
Having a great quality product gives you a big sales boost on Amazon. You get better reviews, fewer returns and usually the Amazon Choice badge goes to high performance products.
In this article we cover the top production issues that usually occur when your products are made by a contract manufacturer.
The best way to guarantee your product is high quality is to arrange an inspection of every shipment even if you have worked with the supplier for a number of months.
Issue 1 Scratches
Small scratches, dents and marks on the product are the most common issues that occur.
You need to allow some tolerance for these defects. If it’s on the back of the product it’s not so critical. If the logo is damaged it’s more noticeable.
Make sure you use AQL as the inspection standard and ask the factory and your inspector to send you a list of major and minor defects to approve. This is basically a list of problems and whether they are classified as major or minor during an inspection.
Issue 2 Glue
You’ll be surprised which products contain glue.
There’s some glue in nearly every product that comes out of a factory from mobile phone cases to bags. As a result there are often glue marks on a product. Or even worse they can have a bad smell.
Get your quality control inspector to watch out for this when checking the products.
Issue 3 Packaging
Provide your factory with clear instructions using step-by-step photos of how you want your product packed.
Get them to test one carton by performing a drop test and vibration test to make sure it won’t damage the goods during shipment.
A vibration test is simply a special machine which shakes the carton to mimic freight transport. A drop test is where the carton is dropped from a certain height to mimic how warehouse workers will throw it around.
Usually the shipping carton will be damaged during these tests, but even if the corner is crunched inwards the contents should still not be damaged and the carton should pass the test.
Issue 4 Labeling
Where stickers or labels are added to the product you need to make sure that the correct label has been added and that it is straight.
Usually stickers are applied by workers by hand. It’s hard to get it exactly right so it is better to use a printed box or insert card instead.
Issue 5 Printing
There are many different types of defect that can come up during the printing of packaging or insert cards.
Ask the factory to send you samples of the packaging before they pack the goods. Double check for any scratches, missing ink, and that the product fits well inside.
Issue 6 Color
To many factories, all blues are blue. They are less strict about the color standard.
You might have ordered a light blue but if you have not given them a specific Pantone color to follow there could be huge variations in the color of your products.
Always specify colors using the international Pantone standard.
Issue 7 Delivery Date
Monitor the estimated delivery date weekly to make sure the goods are on time.
Delays are very common but can be reduced by monitoring what’s happening at the factory.
By regularly checking in you can catch potential issues much faster.